Technical Support Case Study
Case 1
Receive the customer’s inquiries and report of failures → analyze the working conditions and failure mode → apply design optimization solutions → confirm the final design solutions → put into production → acceptance and delivery → follow up and validate
The
valve is designed for applications at a pressure of 22.45mpa, max temperature
of 510℃, a maximum closing pressure difference of 22.45Mpa, an inlet
pressure of 20.52Mpa and an outlet pressure of 0.86Mpa in operation, a working
temperature of 410℃, and an average flow rate of
8000kg/h under normal conditions (half switching time, so the flow rate is
16000kg/h on opening).
The
medium that flows through the valve is LPH high resolution oil residue, with a
density of 1200kg/㎥, a dynamic viscosity of 50mPa·s, a solid content
of 53.6%, and a gasification capacity of 1.5% ~ 10%. The valve core is eroded
by the fluid medium containing solid particles, which leads to valve failure.
According to Preston's grinding empirical formula, the erosion of the valve
plug is proportional to the velocity and pressure of the fluid around the plug.
Case 2
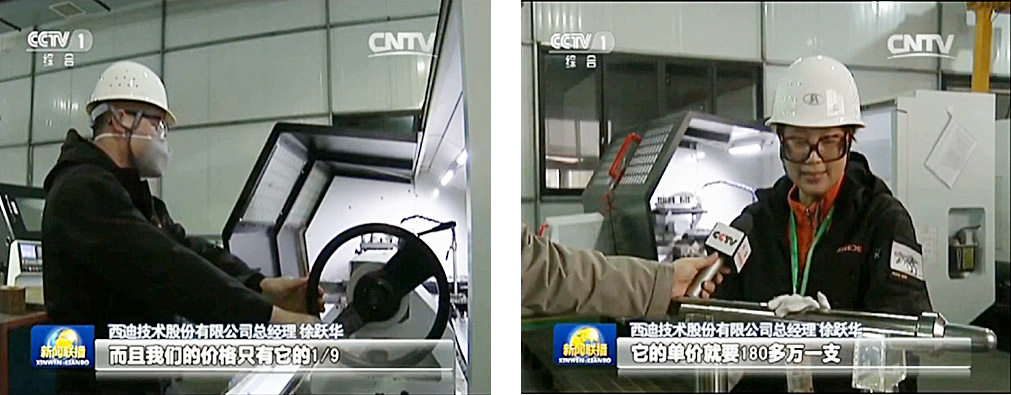
Background :
The demand for petroleum is increasing year after
year, and the reserves of petroleum exploitation are decreasing year after
year. The development of coal-to-oil technology has effectively alleviated this
energy problem. However, the harsh environment faced by coal-to-oil makes its
requirements for materials and equipment very high. As a key core component of
coal-to-oil technology, the demand for one-way valves is growing rapidly, but
the R&D and production of one-way valves was monopolized by Germany in the
early years, the unit price is very high, and the service life is only 1 to 3
hours, all of these were seriously restricting the development of coal
technology.
Solutions :
In order to meet the large demand for
one-way valves from customers in the coal-to-oil field, Seed concentrated on
researching the production technology of one-way valves and evaluated the
independent production of key parts and components of coal-to-oil equipment.
The achievement breaks the monopoly of overseas production and our technology
made a major contribution.
Achievement:
Autonomous production of one-way valves
realizes the reduction of the price to 1/9 of the original, saving costs, and
greatly improving the service life. It was reported by CCTV News Network
"Ingenuity and innovation, showing a new business card of made in
China."